Sunday, January 20, 2013
Using the high-low side driver IR2110 - explanation and plenty of example circuits
In many situations, we need to use MOSFETs configured as high-side switches. Many a times we need to use MOSFETs configured as high-side and low-side switches. Such as in bridge circuits. In half-bridge circuits, we have 1 high-side MOSFET and 1 low-side MOSFET. In full-bridge circuits we have 2 high-side MOSFETs and 2 low-side MOSFETs. In such situations, there is a need to use high-side drive circuitry alongside low-side drive circuitry. The most common way of driving MOSFETs in such cases is to use high-low side MOSFET drivers. Undoubtedly, the most popular such driver chip is the IR2110. And in this article/tutorial, I will talk about the IR2110.
You can download the IR2110 datasheet from the IR website. Here's the download link:
First let’s take a look at the block diagram and the pin assignments and pin definitions (also called lead assignments and lead definitions):
Fig. 1 - IR2110 block diagram (click on image to enlarge)
Fig. 2 - IR2110 Pin/Lead Assignments (click on image to enlarge)
Fig. 3 - IR2110 Pin/Lead Definitions (click on image to enlarge)
Notice that the IR2110 comes in two packages – 14 pin through-hole PDIP package and the 16-pin surface mount SOIC package.
Now let's talk about the different pins.
VCC is the low-side supply and should be between 10V and 20V. VDD is the logic supply to the IR2110. It can be between +3V to +20V (with reference to VSS). The actual voltage you choose to use depends on the voltage level of your input signals. Here’s the chart:
Fig. 4 - IR2110 Logic "1" Input Threshold vs VDD (click on image to enlarge)
It is common practice to use VDD = +5V. When VDD = +5V, the logic 1 input threshold is slightly higher than 3V. Thus when VDD = +5V, the IR2110 can be used to drive loads when input “1” is higher than 3 point something volts. This means that it can be used for almost all circuits, since most circuits tend to have around 5V outputs. When you’re using microcontrollers the output voltage will be higher than 4V (when the microcontroller has VDD = +5V, which is quite common). When you’re using SG3525 or TL494 or other PWM controller, you are probably going to have them powered off greater than 10V, meaning the outputs will be higher than 8V when high. So, the IR2110 can be easily used.
You may lower the VDD down to about 4V if you’re using a microcontroller or any chip that gives output of 3.3V (eg dsPIC33). While designing circuits with the IR2110, I had noticed that sometimes the circuit didn’t work properly when IR2110 VDD was selected as less than +4V. So, I do not recommend using VDD less than +4V.
In most of my circuits, I do not have signal levels which have voltages less than 4V as high and so I use VDD = +5V.
If for some reason, you have signals levels with logic “1” having lower than 3V, you will need a level converter / translator that will boost the voltage to acceptable limits. In such situations, I recommend boosting up to 4V or 5V and using IR2110 VDD = +5V.
Now let’s talk about VSS and COM. VSS is the logic supply ground. COM is “low side return” – basically, low side drive ground connection. It seems that they are independent and you might think you could perhaps isolate the drive outputs and drive signals. However, you’d be wrong. While they are not internally connected, IR2110 is a non-isolated driver, meaning that VSS and COM should both be connected to ground.
HIN and LIN are the logic inputs. A high signal to HIN means that you want to drive the high-side MOSFET, meaning a high output is provided on HO. A low signal to HIN means that you want to turn off the high-side MOSFET, meaning a low output is provided on HO. The output to HO – high or low – is not with respect to ground, but with respect to VS. We will soon see how a bootstrap circuitry (diode + capacitor) – utilizing VCC, VB and VS – is used to provide the floating supply to drive the MOSFET. VS is the high side floating supply return. When high, the level on HO is equal to the level on VB, with respect to VS. When low, the level on HO is equal to VS, with respect to VS, effectively zero.
A high signal to LIN means that you want to drive the low-side MOSFET, meaning a high output is provided on LO. A low signal to LIN means that you want to turn off the low-side MOSFET, meaning a low output is provided on LO. The output on LO is with respect to ground. When high, the level on LO is equal to the level of VCC, with respect to VSS, effectively ground. When low, the level on LO is equal to the level on VSS, with respect to VSS, effectively zero.
SD is used as shutdown control. When this pin is low, IR2110 is enabled – shutdown function is disabled. When this pin is high, the outputs are turned off, disabling the IR2110 drive.
Now let’s take a look at the common IR2110 configuration for driving MOSFETs in both high and low side configurations – a half bridge stage.
Fig. 5 - Basic IR2110 circuit for driving half-bridge (click on image to enlarge)
D1, C1 and C2 along with the IR2110 form the bootstrap circuitry. When LIN = 1 and Q2 is on, C1 and C2 get charged to the level on VB, which is one diode drop below +VCC. When LIN = 0 and HIN = 1, this charge on the C1 and C2 is used to add the extra voltage – VB in this case – above the source level of Q1 to drive the Q1 in high-side configuration. A large enough capacitance must be chosen for C1 so that it can supply the charge required to keep Q1 on for all the time. C1 must also not be too large that charging is too slow and the voltage level does not rise sufficiently to keep the MOSFET on. The higher the on time, the higher the required capacitance. Thus, the lower the frequency, the higher the required capacitance for C1. The higher the duty cycle, the higher the required capacitance for C1. Yes, there are formulae available for calculating the capacitance. However, there are many parameters involved, some of which we may not know – for example, the capacitor leakage current. So, I just estimate the required capacitance. For low frequencies such as 50Hz, I use between 47µF and 68µF capacitance. For high frequencies like 30kHz to 50kHz, I use between 4.7µF and 22µF. Since we’re using an electrolytic capacitor, a ceramic capacitor should be used in parallel with this capacitor. The ceramic capacitor is not required if the bootstrap capacitor is tantalum.
D2 and D3 discharge the gate capacitances of the MOSFET quickly, bypassing the gate resistors, reducing the turn off time. R1 and R2 are the gate current-limiting resistors.
+MOSV can be up to a maximum of 500V.
+VCC should be from a clean supply. You should use filter capacitors and decoupling capacitors from +VCC to ground for filtering.
Now let’s look at a few example application circuits of the IR2110.
Fig. 6 - IR2110 circuit for high-voltage half-bridge drive (click on image to enlarge)
Fig. 7 - IR2110 circuit for high-voltage full-bridge drive with independent switch control (click on image to enlarge)
In Fig. 7 we see the IR2110 being used to drive a full bridge. The functionality is simple and you should understand it by now. A common thing that is often done is that, HIN1 is tied/shorted to LIN2 and HIN2 is tied/shorted to LIN1, enabling the control of all 4 MOSFETs from 2 signal inputs, instead of 4 as shown below in Fig. 8.
Fig. 8 - IR2110 circuit for high-voltage full-bridge drive with tied switch control - control with 2 input signals (click on image to enlarge)
Fig. 9 - Using the IR2110 as a single high-voltage high-side driver (click on image to enlarge)
In Fig. 9 we see the IR2110 being used as a single high-side driver. The circuit is simple enough and follows the same functionality described above. One thing to remember is that, since there is no low-side switch, there must a load connected from OUT to ground. Otherwise the bootstrap capacitors can not charge.
Fig. 10 - Using the IR2110 as a single low-side driver (click on image to enlarge)
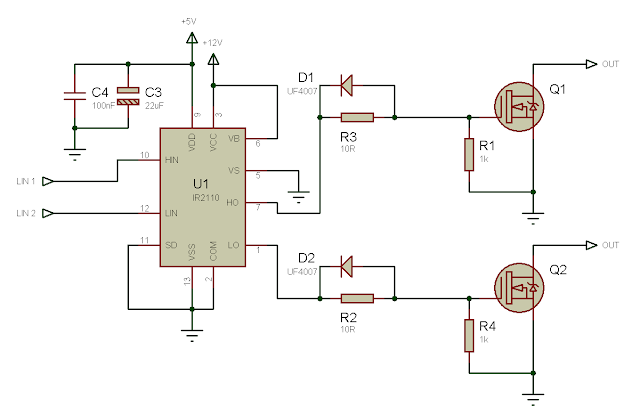
Fig. 11 - Using the IR2110 as a dual low-side driver (click on image to enlarge)
--------------------------------------------------------------------------------------------------------------------------------------------------------------------------------------------------------------
If you've had failures with IR2110 and had driver after driver, MOSFET after MOSFET get damaged, burn and fail, I'm pretty sure that it's due to you not using gate-to-source resistors, assuming of course that you designed the IR2110 driver stage properly. NEVER OMIT THE GATE-TO-SOURCE RESISTORS. If you're curious, you can read about my experience with them here (I have also explained the reason that the resistors prevent damage):
For further reading, you should go through this:
I have seen in many forums that people struggle with designing circuits with IR2110. I too had a lot of difficulty before I could confidently and consistently build successful driver circuits with IR2110. I have tried to explain the application and use of IR2110 thoroughly through explanation and plenty of examples and hope that it helps you in your endeavors with IR2110.
|